What’s next in the digitalisation of logistics? FedEx shares its vision and move to pre-operational intelligence.
IRU member FedEx is embracing digitalisation – from predictive algorithms and solar panel-powered GPS devices to digital customs processes – to improve every facet of its operations.
We asked Mark Timmermans, Vice President Network Planning & Engineering at FedEx, to give us some insights into the company’s latest digitalisation advancements.
How has digitalisation improved your operations?
The FedEx approach to data and digitalisation is both practical and ambitious. Our ambition is to become a leader in supply chain technology. Our global technology investments focus on optimising our own operations, digitalising our customers’ supply chains, and enhancing the e-commerce customer experience.
In our European road network, a key focus is on finding new approaches, through predictive analytics and other technologies, to make sure we operate the network in the most efficient, reliable way. All our trailers are equipped with solar panel-powered GPS devices to track our movements across Europe. This enhances the security of our customers’ shipments while allowing us to maximise operational planning.
We are now also integrating our data with other sources to fully leverage its value and apply it in new ways. We have launched an application that allows us to have a full view on what’s being transported in the trailers we operate across our network. This means our sorting locations can optimise their resources and capacity planning as they can see what’s coming their way and how it is loaded. As the data and corresponding decisions accumulate, the system “learns” and offers suggestions or predictions for appropriate actions.
Improved levels of intelligence on each package travelling through our road network means we can also better plan our last-mile deliveries and use our delivery fleet more intelligently.
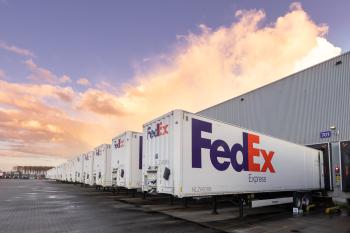
Which emerging technologies are you exploring?
Already in 1978, our founder, Fred Smith, said, “The information about the package is just as important as the package itself.” Fifty years later, we are in the midst of a digital revolution, moving from post-operational intelligence to live and pre-operational intelligence.
Our vast physical network is a rich source of data. We deliver nearly 17 million parcels daily and generate over 1 petabyte of data every day. By leveraging this data, we increase real-time insights and make delivery predictions, allowing our customers to intervene in their supply chain if needed.
We have developed FedEx Surround: an AI-powered monitoring tool that combines sensor and weather data to predict disruptions, enabling customers to take proactive action.
A FedEx proprietary technology we launched during COVID-19 is SenseAware. It brings active sensors to the FedEx network to improve real-time visibility and custodial control, whether for vaccine distribution or other critical shipments.
Another example is the FedEx Sustainability Insights tool. It provides customers a self-service tool, accessible online, to view and download reports that estimate the CO2 equivalent of their shipments as they pass through the FedEx network.
We also use AI to better and more efficiently manage volume flows within our operational networks, as well as predictive algorithms to forecast peak volumes. This allows us to proactively plan resources and personnel to meet fluctuating demand.
In our ground operations, we believe that autonomous vehicle technology is promising and has the potential to impact transport at all levels in the future – from long-haul to last-mile delivery. We have been actively testing autonomous vehicles in the US, and we support more testing and research to advance transport technologies that improve safety and efficiency for all drivers.
We also view the testing and adoption of technology and automation as an opportunity to increase safety, improve productivity and provide training and career opportunities for FedEx teams.
In 2021, FedEx entered into a tri-party collaboration with Aurora Innovation – a leading autonomous technology company – and PACCAR – one of the largest medium-and-heavy-duty vehicle manufacturers in the world – to test Aurora’s autonomous driving technology in PACCAR vehicles within FedEx linehaul trucking operations. Aurora continues to move shipments for FedEx in Texas daily with safety drivers on board.
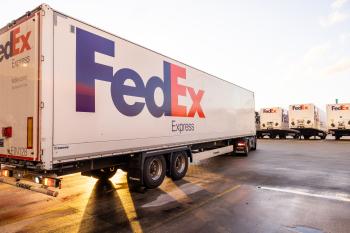
Where do you see impactful digitalisation efforts in road transport?
An area where we see significant progress towards increased digitalisation is customs. With the EU’s Union Customs Code (UCC) coming into play, driving the industry to more harmonisation of clearance systems across the continent, technology and tools have been developed to support the move from manual paperwork to digital solutions. The most recent developments in this area have been around upgrading our systems to incorporate Release 3 of ICS2. While we were already complying with the regulations for goods shipped into or transiting the EU by air, we are now also compliant for other modes of transport, including road transport.
FedEx uses a range of practical tools, technologies and services that offer businesses a digital solution to deal with trade rules and compliance. These tools range from generating customs documentation to sharing information about prohibited or restricted items and automating the process of calculating duties and taxes. Customers who use these solutions instead of manual paperwork are experiencing significantly better clearance performance. We encourage our customer base to adopt these tools.
Our real-time tracking tools provide visibility into shipments as they move through customs, including the option of proactive updates in case of delays or issues. These tools also allow our customers to manage duty and tax payments while goods are still in transit, ensuring that shipments clear customs without delays, while enabling a smoother delivery experience.
Which digital solutions should be prioritised in the coming years?
There is great potential to further reduce customs bureaucracy for businesses if we embrace digital technologies to reduce trade friction. Trade relies on processes that are simple, streamlined and interoperable between different systems.
This is where plans for a new EU customs data hub could change the game. Having a single, centralised data portal would strengthen customs processes, reduce fraud, and give traders just one IT environment to register and clear goods. Everyone benefits from a system that is simpler, faster and more reliable.